ISO-Compliant Receiving Process: A Deep Dive into Standards, Systems, and Strategic Execution
Introduction: The Receiving Dock as a Strategic Control Point
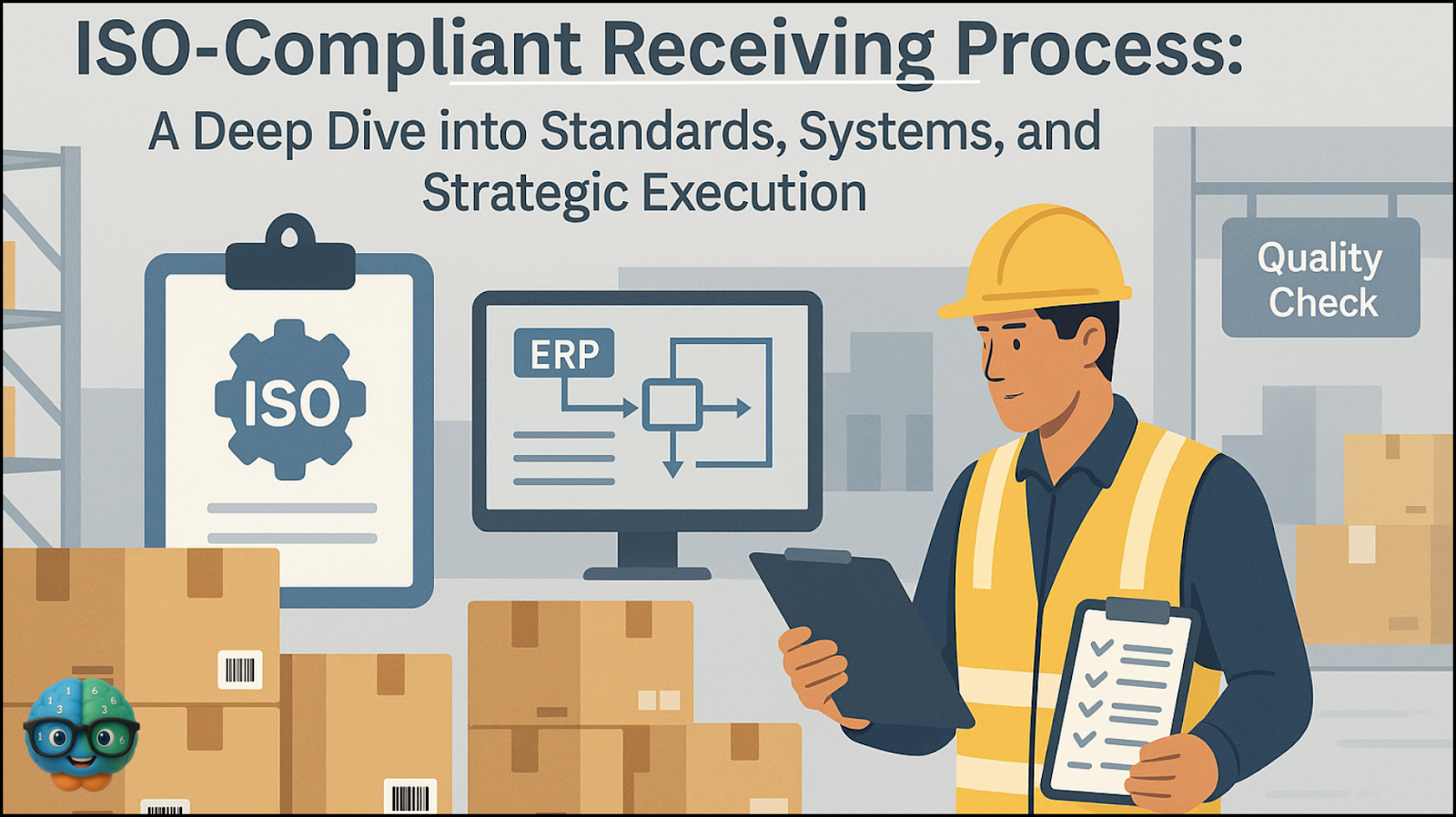
The receiving dock is far more than a logistical checkpoint—it’s the first and often the most critical quality assurance node in the supply chain. For ISO-aligned businesses, this process is foundational. It ensures goods arriving from suppliers are accurate, undamaged, compliant, and fit for purpose. In ISO 9001-certified environments, receiving isn’t merely about checking quantities; it’s about verifying supplier performance, initiating traceability, and ensuring enterprise-wide quality alignment. This article unpacks the ISO-compliant receiving process in detail and introduces a fully structured Excel tool that can be used to track and enforce compliance.
Index
- Foundations: ISO 9001 and Its Application to Receiving
- Strategic Roles in the Receiving Process
- Step-by-Step: ISO-Aligned Receiving Process
- Tracker Sheet Design: Digital Twin of Warehouse Activity
- Supporting Technologies
- Toyota Case Study: Excellence in Execution
- Common Pitfalls and Field-Based Fixes (Tools)
- Conclusion: The Dock is Where Excellence Begins
- Appendix: Tools & Templates
1. Foundations: ISO 9001 and Its Application to Receiving
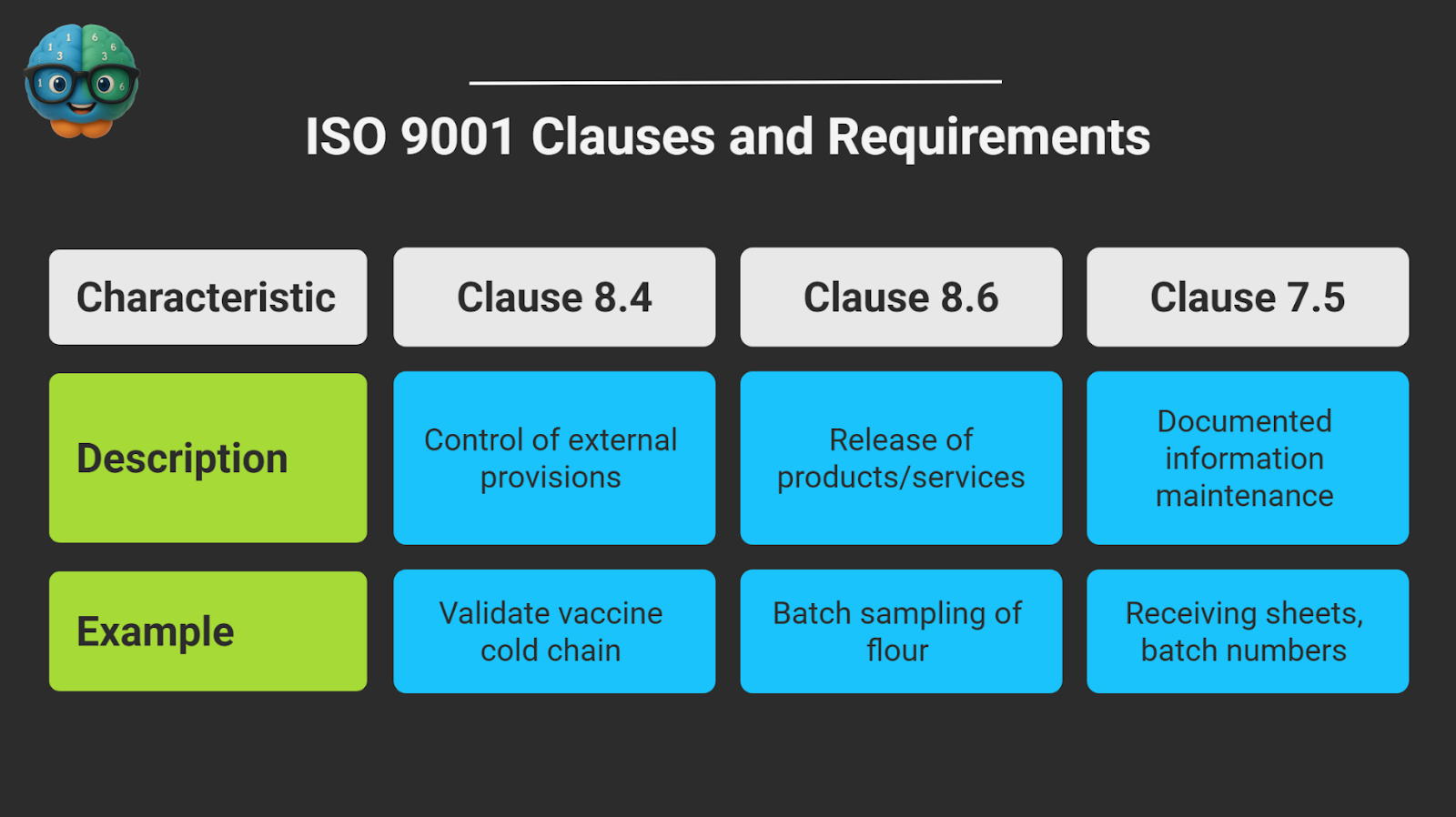
The ISO 9001:2015 standard defines the foundational elements of a Quality Management System (QMS). It emphasizes the importance of documented procedures, traceability, verification, and continuous improvement. In the context of receiving operations, three clauses are particularly relevant:
- Clause 8.4 – Control of Externally Provided Processes, Products, and Services: Requires businesses to ensure that externally sourced goods and services meet specified criteria before acceptance. Example: A medical supplier receiving temperature-sensitive vaccines must validate cold chain records upon delivery.
- Clause 8.6 – Release of Products and Services: Mandates that organizations conduct appropriate inspections and testing prior to releasing products into inventory or production. For instance, a food manufacturer may require batch-level sampling before storing a flour shipment.
- Clause 7.5 – Documented Information: Requires organizations to maintain accessible and accurate records. This includes signed receiving sheets, batch numbers, NCR logs, and digital timestamps in ERP systems.
These clauses create a framework that places responsibility not just on quality departments but also on warehouse teams, procurement officers, and even IT system architects. Designing the right tools and system processes that can support the company specific operations is crucial.
2. Strategic Roles in the Receiving Process
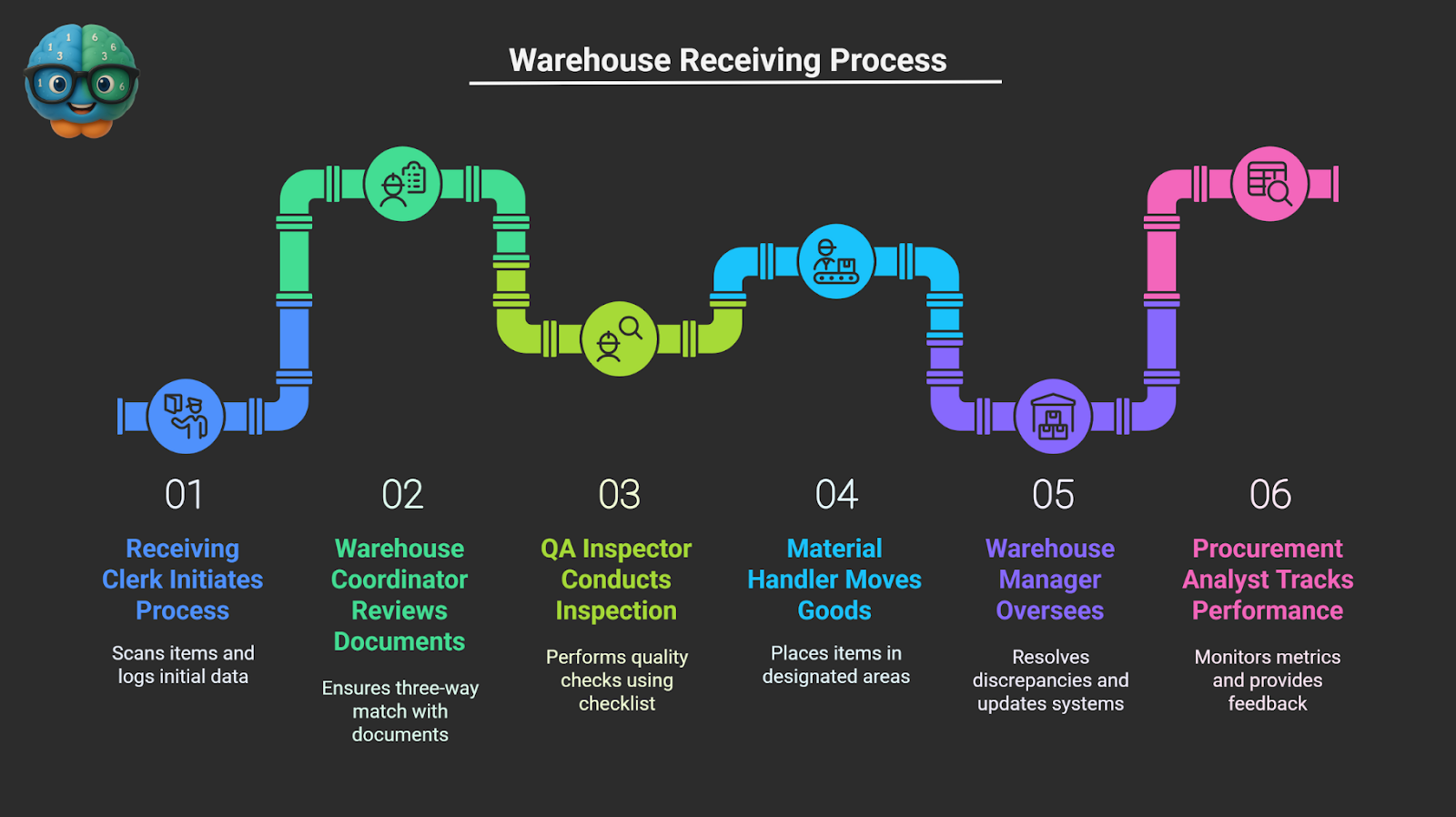
Receiving operations require coordination among multiple stakeholders. Quality assurance cannot be siloed within the QA team; it must be distributed through systems and personnel.
- Receiving Clerk: Initiates the receiving process by scanning items using barcodes or manual entry information in a Receiving sheet. The receiver temporarily stores the shipment in Staging Area. Logs initial data such as time of delivery, quantity, and packaging condition and escalates the process to the Warehouse Coordinator.
- Warehouse Coordinator: Reviews documentation (COA, ASN, packing list), ensures three-way match with Purchase Order, Packing List/Delivery Note, and Invoice. Further escalating the receiving process to QA inspector for final clearance before the received goods are moved into Bin Locations.
- QA Inspector: Conducts sampling inspection, dimensional or functional checks depending on product criticality using a standard Quality Receiving Checklist. Advise Warehouse Coordinate to proceed and place the received shipment into either warehouse bin locations or QA Hold Locations.
- Material Handler: A Material handler in the warehouse moves the received shipment in the warehouse and places them into different areas depending on the Inventory Management System and Inventory Policy.
- Warehouse/Inventory Manager: Oversees resolution of discrepancies, final sign-off, NCR management, and facility communication between different stakeholders of the business depending on the type of discrepancies, conflict resolution, or reporting. Updates inventory systems. The inventory Management System (IMS) further directs internal operations like Production, Procurement, Sales, etc.
- Procurement/Supplier Performance Analyst: Tracks performance metrics across multiple shipments and issues supplier feedback or corrective requests.
Together, these roles prevent blind spots and ensure traceable, auditable workflows.
3. Step-by-Step: ISO-Aligned Receiving Process
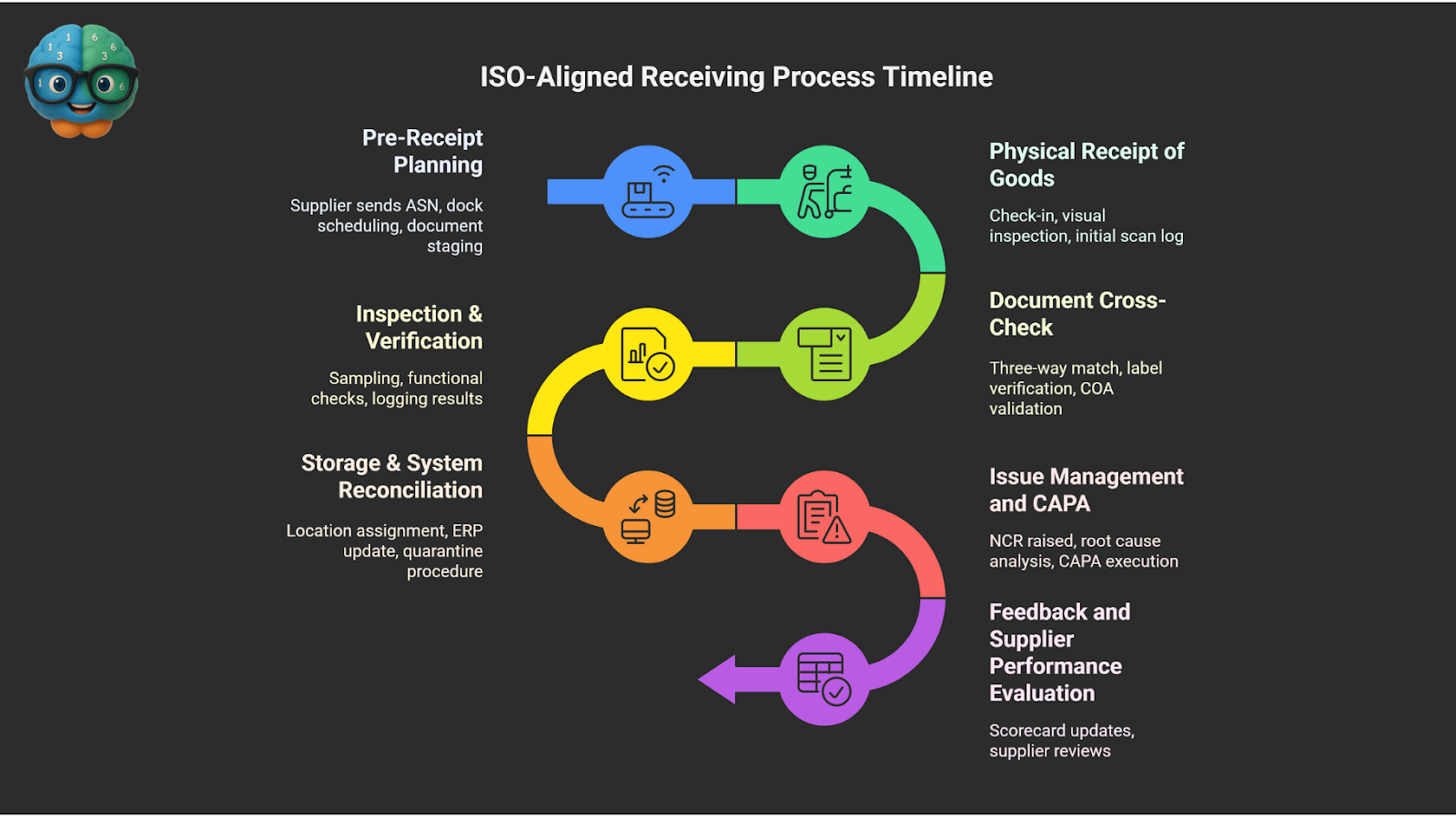
To illustrate how ISO standards apply practically, we walk through a structured sequence of events—each mapped to specific system entries and personnel responsibilities.
3.1 Pre-Receipt Planning
- Advance Shipping Notice (ASN): Supplier sends a digital preview of the shipment including PO number, SKUs, and expected arrival time.
- Dock Scheduling: Receiving team allocates space and resources to prevent bottlenecks.
- Document Staging: Certificates of Analysis (COAs), Safety Data Sheets (SDS), and packing lists are preloaded into the system.
3.2 Physical Receipt of Goods
- Check-In: Upon arrival, clerk logs the shipment in the ERP/WMS and performs initial scanning.
- Visual Inspection: Checks for packaging damage, proper labeling, and barcode readability.
- Initial Scan Log: Automatically or manually matched against ASN and PO.
3.3 Document Cross-Check
- Three-Way Match: Purchase Order, Packing List, and Invoice list must align.
- Label & Batch Verification: Ensures batch codes and expiration dates match internal requirements.
- COA Validation: Confirms test results and compliance certificates.
- Sampling: Based on risk level and statistical sampling plans like ANSI Z1.4.
- Functional Checks: Performed on high-risk or regulated goods.
- Logging: Results recorded in tracker and/or QMS software.
- Location Assignment: Product assigned to bins, racks, or special storage.
- ERP Update: Marks the items as received and available.
- Quarantine Procedure: If goods are suspect, they’re held until cleared by QA.
- NCR Raised: Non-conformance report generated.
- Root Cause Analysis: Led by QA or quality manager.
- CAPA Execution: Documented and shared with suppliers.
3.4 Inspection & Verification
- Sampling: Based on risk level and statistical sampling plans like ANSI Z1.4.
- Functional Checks: Performed on high-risk or regulated goods.
- Logging: Results recorded in tracker and/or QMS software.
3.5 Storage & System Reconciliation
- Location Assignment: Product assigned to bins, racks, or special storage.
- ERP Update: Marks the items as received and available.
- Quarantine Procedure: If goods are suspect, they’re held until cleared by QA.
3.6 Issue Management and CAPA
- NCR Raised: Non-conformance report generated.
- Root Cause Analysis: Led by QA or quality manager.
- CAPA Execution: Documented and shared with suppliers.
3.7 Feedback and Supplier Performance Evaluation
- Scorecard Updates: Includes quality, delivery accuracy, and issue resolution time.
- Supplier Reviews: Quarterly review meetings held with strategic suppliers.
4. Tracker Sheet Design: Digital Twin of Warehouse Activity
A receiving tracker should not only record information—it should guide actions. Fields must map to user roles and ISO requirements.
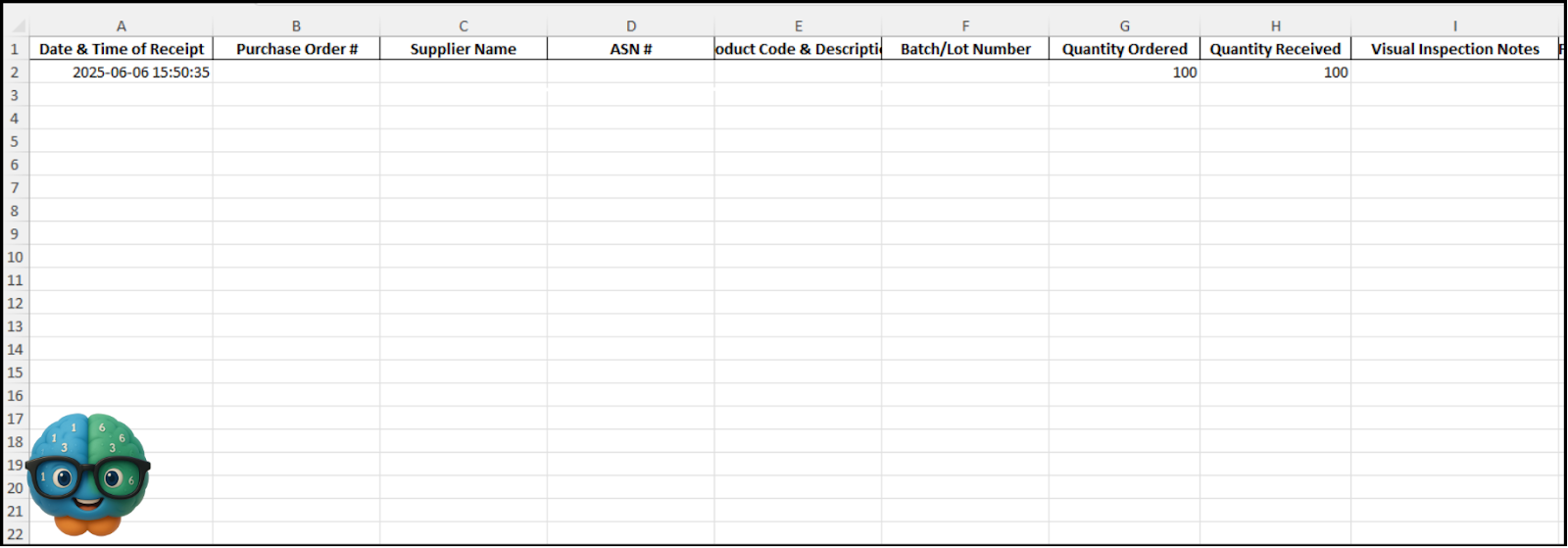
Field Name | Purpose | Owner |
---|---|---|
Date & Time of Receipt | Traceability | Receiving Clerk |
PO Number | Links to procurement | Clerk |
Supplier Name | Supplier traceability | Clerk |
ASN # | Confirm expected delivery | Coordinator |
Product Code & Description | Confirms line item | Clerk |
Batch/Lot Number | Enables traceability | QA |
Quantity Ordered vs Received | Discrepancy check | Clerk |
Visual Condition | Notes any damage | Clerk |
Inspection Results | Accept/Reject, reason | QA |
NCR Raised | Yes/No | Coordinator |
Storage Location | Inventory slot | Coordinator |
Inspection Completed By | Quality validation | QA |
Verified By | Final reviewer | Manager |
Follow-Up Actions | Links to CAPA | QA/Procurement |
Comments | Notes for audit or trace | Any |
Following is an example of Tracker Sheet that can be used as a template or used as it is for tracking warehouse activities.
5. Supporting Technologies
- ERP/WMS Systems: For automation, role-based workflows, and batch tracking.
- Barcode & RFID Scanners: Speed up data entry and error detection.
- Digital COA Integration: Prevents manual errors and ensures compliance.
- QMS Platforms: For NCR, CAPA, audits, and ISO documentation.
6. Toyota Case Study: Excellence in Execution
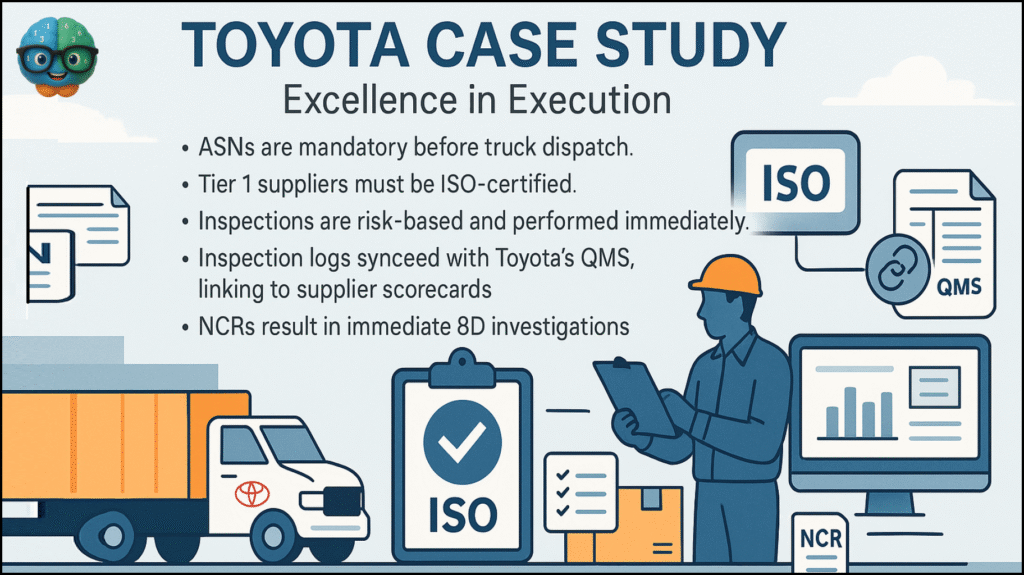
Toyota’s Just-in-Time model depends on flawless receiving. Here’s how they integrate ISO standards:
- ASNs are mandatory before truck dispatch.
- Tier 1 suppliers must be ISO-certified.
- Inspections are risk-based and performed immediately.
- Inspection logs are synced with Toyota’s QMS, linking to supplier scorecards.
- NCRs result in immediate 8D investigations.
This integration ensures that no defect flows downstream to production. Read the complete case study in a dedicated article below.
7. Common Pitfalls and Field-Based Fixes (Tools)
Pitfall | Prevention Strategy |
---|---|
Manual-only tracking | Use hybrid digital-physical trackers |
No barcode system | Implement low-cost mobile scanners |
Missing COAs or SDS | Require ASN-linked uploads before shipment |
Role ambiguity | Define tasks via SOPs and digital permissions |
Delayed discrepancy resolution | Integrate NCRs into procurement dashboards |
8. Conclusion: The Dock is Where Excellence Begins
ISO standards set the minimum expectations—but leaders set new benchmarks. At Brilliant Supply Chain, we see the receiving process as a control tower: it governs quality, flow, visibility, and accountability.
When executed correctly, it:
- Prevents defects from entering production
- Holds suppliers accountable
- Powers data-driven improvement
- Creates audit-ready transparency
- Strengthens inventory integrity
Appendix: Tools & Templates
- Excel-Based Receiving Log
- NCR Template
- CAPA Form
- Supplier Performance Scorecard
- Receiving SOP Template
- ANSI Z1.4 Sampling Plan Reference
For implementation support, custom tracker design, or QMS integration, contact the Brilliant Supply Chain consulting team.